The testing equipment is a kind of tool for scientific research. Due to the rapid development of information technology, the data acquisition and electro-hydraulic control part of the testing equipment produced around the end of last century generally needs to update. At the same time, the mechanical part is still in good condition.
If the testing equipment is not timely updated, the failure rate of the equipment will be high. This may cause damage of the specimen, and increase the danger of the operator, increase the scientific research cost and data error possibility. If the testing equipment is discarded directly for the reason of backward technology and high failure rate, the machinery part which may account for more than half of the cost and can work properly will also be discarded. This will cause waste and not meet the requirements of build modern saving society.
Based on the experience from practice and cooperation with different kind of customers, Popwil established a technical route to upgrade the old generation of testing equipment with outdated technology and good mechanical parts such as the multi-channel loading system from MTS, the static-dynamic universal testing machine from MTS and Instron, the large scale press testing machine etc.
The picture below is a photo of a teaching testing system of Hong Kong Polytechnic University before upgrade. It does loading by manually operated jack.
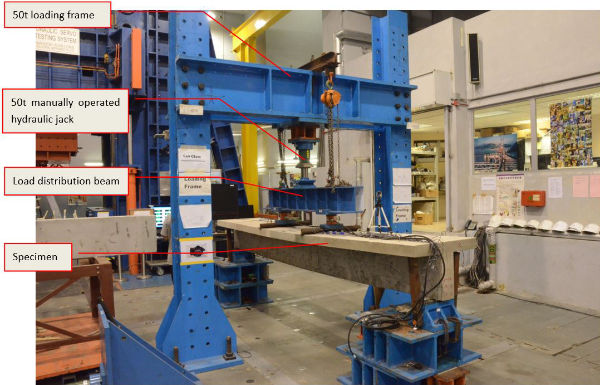
The teaching testing system of Hong Kong Polytechnic University
The follow picture is the upgraded teaching testing system of Hong Kong Polytechnic University. The manual operated hydraulic loading jack is replaced by an electro-hydraulic servo controlled actuator, and at the same time, the IPC controller can do testing data acquisition automatically.
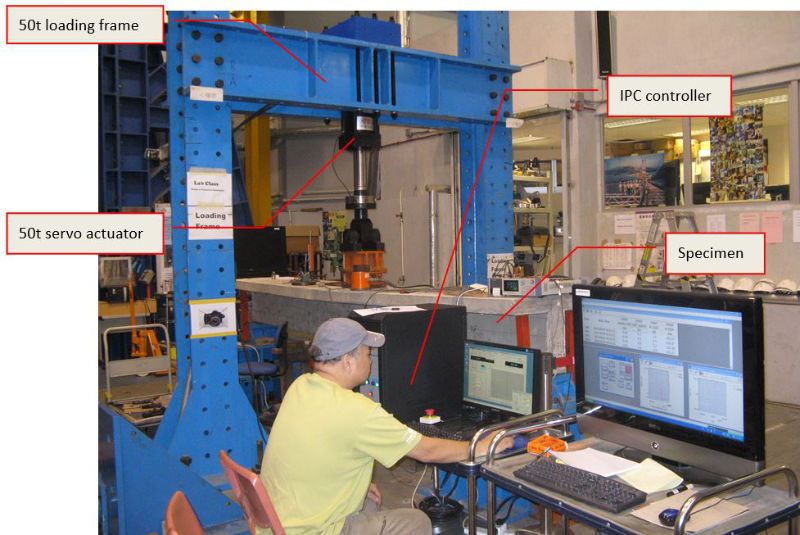
The teaching testing system after upgrade
Next picture is a 2400t rubber bearing compress-shear testing system. The customer is Doshin Rubber Products (M) SDN. BHD.
Before Popwil doing upgrade, this large scale testing machine was designed to perform close loop control by a PLC controller. Both vertical loading accuracy and horizontal loading speed cannot meet the requirements of the testing standard. Popwil make use of double channel POP-M servo controller instead of PLC to do data acquisition and close-loop control. The upgraded new system accomplished the rubber bearing compress-shear test and meet the requirements of the testing standard.
The follow picture is the photo of the main frame of the e-lab 200 when Popwil sign the contract. The previous supplier only finished the installation of the main frame.
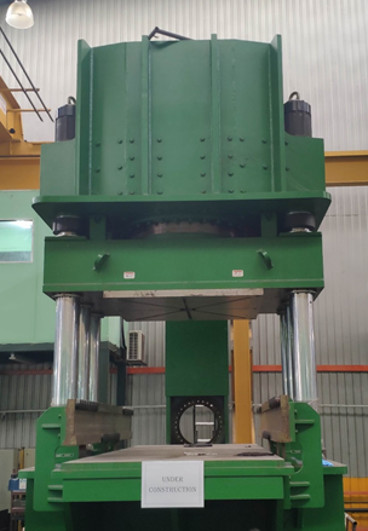
The e-lab 200 before upgrade
In this project, Popwil finished the construction of the main frame, the horizontal loading system and the hydraulic servo control system. The picture after upgrade is as follow.
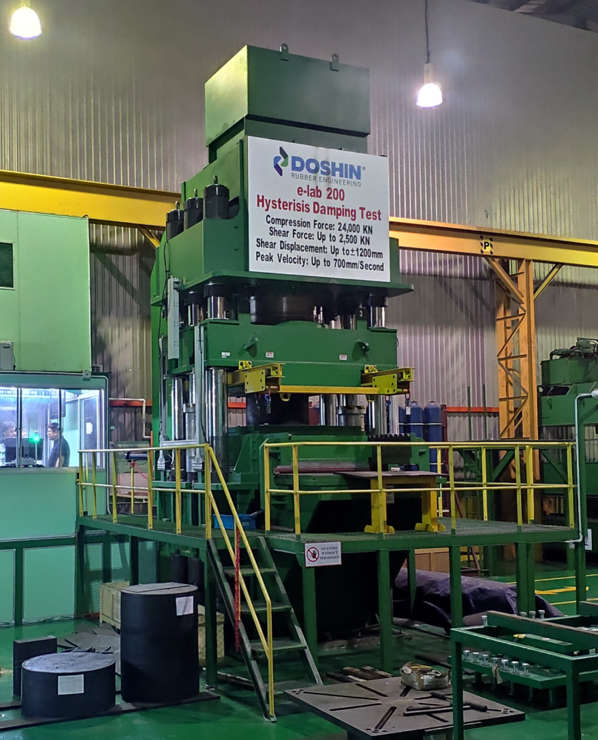
The front view of the e-lab 200 after upgrade
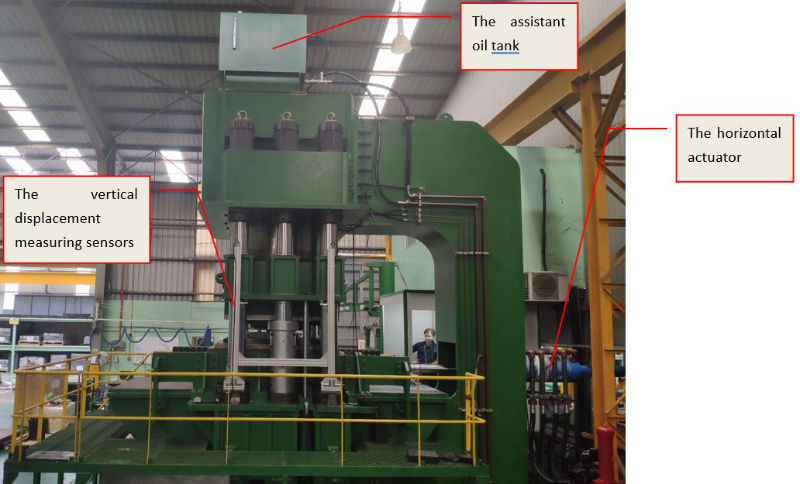
The side view of the e-lab 200 after upgrade
After the upgrade, a displacement measurement system and a horizontal shear servo actuator were added. The POP-M electro-hydraulic servo multi-channel IPC controller was used to do data acquisition and close loop control during the test. The control and measuring precision is met the requirements both from the testing standard and the customer.
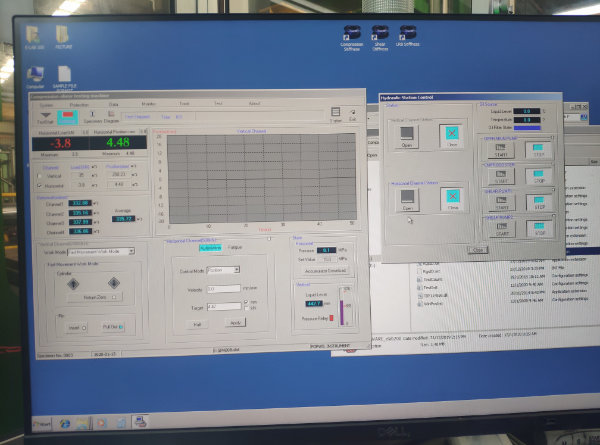
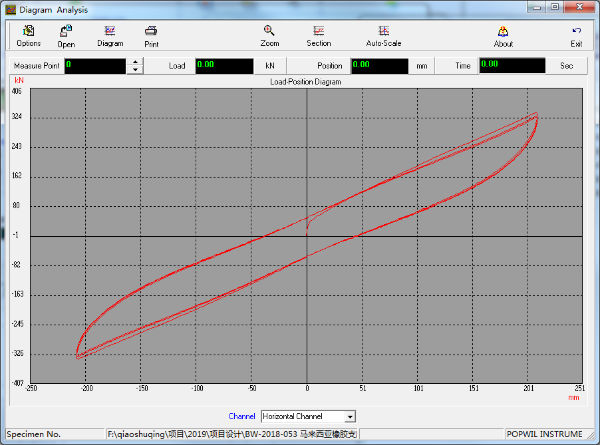
The software interface of POP-M controller for e-lab 200
The main technical parameters after the UPGRADING are as follows:
- Maximum vertical load: 24000kN;
- Vertical test force control mode: electro-hydraulic servo closed-loop control loading and load holding;
- Vertical load holding control accuracy: 2% of set value;
- Horizontal load: +/- 500kN;
- Horizontal displacement: +/- 300mm;
- Horizontal actuator stroke: +/- 500mm, rod end connecting disc is connected with sliding plate;
- Maximum horizontal piston stroke speed: 600mm / s;
- Waveform: sine wave;
- Cycle: up to 10.